27. 8. 2014
Významné zvýšení bezpečnosti práce při vytěsňování
hořlavých plynů a kapalin i při odvzdušňování plynovodů skýtá
použití inertizační směsi s vysokým obsahem dusíku. Díky tomu
nehrozí žádné riziko vzniku výbušné směsi v potrubí a tedy ani
riziko výbuchu.

Generátor dusíku při přepravě na
staveniště
Pro tuto technologii vyvinul CEPS generátor dusíkové inertizační
směsi na bázi membránové separace a po jejím úspěšném provozním
odzkoušení pořídil další technologickou řadu s výstupním
tlakem až 25 barů.
Vyprazdňování potrubí s hořlavými plyny a kapalinami
pomocí vzduchu má svá rizika
Jednou z bezpečnostně závažných operací při uvádění
plynovodů do provozu nebo jejich odstavování je odvzdušňování a
odplyňování. Při těchto operacích dochází na rozhraní plyn/vzduch
ke vzniku směsi s koncentrací plynu ve vzduchu mezi horní a
dolní mezí výbušnosti, tzv. výbušné směsi.
U potrubí dopravujících hořlavé kapaliny, jako ropu, naftu nebo
benzin, je situace ještě komplikovanější, protože výbušná směs
vzniká nejen při samotném vytlačování přímo na rozhraní
vzduch-médium, ale následně vzniká v celém vyprázdněném
objemu, protože do vzduchu se odpařují hořlavé složky, které i po
vyprázdnění ulpívají v kapalné formě na stěně potrubí.
Řešením problému je použití inertních plynných
směsí
Ze všech důvodů uvedených v předcházející části přistoupila
řada provozovatelů ve světě k náhradě vzduchu při odplyňování
inertizačním plynem, jímž je zpravidla dusík. V případě
vyprazdňování ropovodů a produktovodů se používá inertizační směs
prakticky vždy, což předepisuje i evropská norma EN 14161(Naftový a
plynárenský průmysl - potrubní přepravní systémy).
Hlavním přínosem použití inertizační plynné směsi je fakt, že zóna
výbušné směsi vůbec nevzniká, a proto je možnost exploze zcela
vyloučena. Výhodou této technologie je rovněž skutečnost, že po
vytlačení média je vnitřek potrubí naplněn inertním dusíkem, takže
nehrozí jakékoli riziko exploze jinak výbušných a hořlavých plynů
nebo uhlovodíkových par.
Vytváření inertizační směsi z kapalného
dusíku
Ve světě je pro vyprázdnění potrubí převážně používána
technologie založená na využití kapalného dusíku. Podstatou této
technologie je vytlačování plynu nebo kapalného média
prostřednictvím dusíku, který se přivádí na začátek vyprazdňovaného
úseku. Kapalný dusík se na začátek potrubí dopraví v hluboce
podchlazeném stavu (zhruba - 180 ºC) pomocí kryogenních cisteren,
ve speciálním zařízení se dusík stlačí a následně odpaří. Vzniklý
tlakový dusík se pak vede do potrubí a prostřednictvím čisticího
pístu vytlačuje médium na druhý konec vyprazdňovaného úseku. Tato
technologie má však také určité nevýhody:
- značná spotřeba energie pro výrobu kapalného dusíku
zkapalňováním vzduchu,
- poměrně dlouhotrvající příprava akcí - větší množství kapalného
dusíku je třeba zpravidla objednávat s dostatečným předstihem,
stejně jako zajištění přepravních cisteren,
- odpaření kapalného dusíku vyžaduje speciální výkonné odpařovací
hořáky spalující velké množství nafty,
- kryogenní přepravní cisterny jsou převážně v silničním
provedení, a proto jen obtížně dojedou do míst trasových uzávěrů,
která jsou zpravidla přístupná jen lehkými nebo terénními
automobily. Takové případy je pak třeba řešit výstavbou dočasného
potrubí pro dopravu plynného dusíku od cisterny/odpařovače
k trasovému uzávěru nebo zpevněním cest.
Technologie vyprazdňování pomocí dusíku dováženého
v kapalné formě je tedy organizačně, nákladově a
energeticky poměrně velmi náročná.
Výroba inertizační směsi ze vzduchu na místě
použití
S přihlédnutím ke skutečnosti, že dusík je složkou vzduchu
nepodporující dýchání ani hoření, společnost CEPS v letech
2010-11 odzkoušela a ověřila jinou metodu, která zásadní nevýhody
vyprazdňování potrubí ropovodů a produktovodů vzduchem nebo
regazifikovaným kapalným dusíkem eliminuje. Tato metoda používá pro
vytlačování média inertizační dusíkovou směs, která se však
připravuje přímo na místě užití na začátku vyprazdňovaného úseku a
to membránovou separací ze vzduchu. Výhodou tohoto procesu je
skutečnost, že dusíku ve vzduchu na místě použití je "nekonečně
mnoho", a proto je možné inertizovat prakticky jakýkoli objem,
zatímco při použití kapalného dusíku je nutné dovézt každý kubík,
podle lokality často i ze vzdálenosti několika set kilometrů, a to
inertizaci větších objemů potrubí velmi prodražuje.
Při membránové separaci se vzduch stlačí v kompresoru na cca
16 barů a vede se do membránové separační jednotky, v níž se
díky různé permeabilitě membrány vůči kyslíku a dusíku ze
stlačeného vzduchu separuje dusík o čistotě přes 90 %. Tato hodnota
čistoty dusíku byla převzata z podnikové normy ruského
největšího přepravce ropy Transněfť, který je i jedním z největších
přepravců ropy a ropných produktů na světě. Použití této
technologie není principielně technickou novinkou, běžně se používá
v průmyslových závodech nebo na ropných tankerech při jejich
vyprazdňování. Zásadně nový však byl požadavek "miniaturizace"
zařízení tak, aby bylo snadno přepravovatelné i v těžkém
terénu, limitem tedy byl objem standardního kontejneru ISO 20 ft.
(délka 6 m, šířka i výška 2,5 m) a hmotnost do 7 tun. Navíc celé
zařízení musí být energeticky soběstačné a jediným potřebným médiem
smí být motorová nafta.
Od myšlenky k prototypu
Prototyp generátoru dusíku navrhl a vyrobil CEPS na vlastní
náklad ve spolupráci s několika dílčími dodavateli. Od samého
počátku byl prototyp vyvíjen tak, aby ho bylo možné snadno
dopravovat na větší vzdálenosti i v náročném terénu (viz obr.
1).
Zařízení pracuje v automatickém režimu řízeném počítačem,
počínaje čištěním a předehřevem procesního vzduchu až po regulační
armatury na výstupu inertizační směsi, jejíž složení je
nastavitelné ve třech úrovních - 90 %, 93 % a 95 % dusíku. Volba
úrovně koncentrace dusíku závisí na typu vytlačovaného média a na
tlaku, který je pro vytláčení potřebný.
Od prototypu k výkonnější jednotce
Úspěšně dokončený vývoj generátoru inertizační směsi a okamžitý
zájem provozovatelů potrubních systémů o tuto službu nás vedl
k rozhodnutí tuto technickou novinku rozšířit. Návrhové
parametry další jednotky jsme definovali podle typických provozních
podmínek při vytlačování hořlavých kapalin v běžných
evropských podmínkách a v reálně potřebných časech.
Jako definiční podmínky byly zvoleny požadované provozní
charakteristiky vyprázdnění ropovodu DN 700 IKL v typicky
západo- a středočeském kopcovitém terénu.
Analýza spotřeby energie v typických provozních režimech pak
vedla k definici uspořádání jednotky tak, že procesní vzduch
bude stlačen v kompresoru na 16 barů a veden do jednotky
separace dusíku. Vytvořená inertizační směs s tlakem minimálně
10 barů bude stlačena dalším kompresorem - boosterem na minimálně
23 barů.
Z přepravních důvodů (opět byl stanoven požadavek na
zabudování generátoru dusíku i boosteru do ISO 1C 20 ft.
kontejnerů) bylo nutné řetězec rozdělit do dvou zcela identických
řad.
V roce 2012 podal CEPS přihlášku do operačního programu
Podnikání a inovace, který tento typ technologických inovací
podporuje. V rámci programu Inovace - Inovační projekt - Výzva
IV byl CEPS pro udělení podpory vybrán a náš projekt číslo 4.1
IN04/944 získal podporu ve výši 60 %. Zbývajících 40 % musel CEPS
vložit z vlastních zdrojů. Náročné cash-flow projektu, které
je důsledkem dotačního systému, kdy jsou zpětně pokrývány jen již
vynaložené prostředky, se podařilo vykrýt díky sofistikovanému
úvěrovému programu vytvořeném ve spolupráci s naší financující
pobočkou ČSOB Tábor.
Vzhledem k tomu, že v rámci financování byly využity
veřejné prostředky, bylo na dodávku kompletního řetězce vypsáno
veřejné výběrové řízení se všemi náležitostmi. Jen zadávací
dokumentace zahrnovala 29 stran. Z několika uchazečů nakonec
naplnila podmínky pouze česká společnost Acstroje, s. r. o.
Jablonec nad Nisou.
Dodavatel Acstroje realizoval řetězec se třemi hlavními
subdodavateli. Zatímco dokumentace samotného generátoru dusíku byla
k dispozici prakticky kompletní z fáze výroby prototypu,
boostery bylo třeba navrhnout a zkompletovat opět jako kusovou
dodávku. Finálním řešením v každé z obou jednotek jsou
dva kompresory (viz obr. 3) ve společné regulaci . Na rozdíl od
primárních kompresorů procesního vzduchu, které mají pochopitelně
pohon dieselovými motory, kompresory boosterů mají elektropohon
(každý 22 kW), a proto musí být každá jednotka vybavena
elektrocentrálou s poměrně značným výkonem 80 kVA, neboť
musí být schopna pokrýt i rozběhové proudy motorů.
Každá z obou řad technologického řetězce je samostatně
zásobována procesním vzduchem prostřednictvím kompresoru Atlas
Copco XRHS 506 (viz obr. 4).
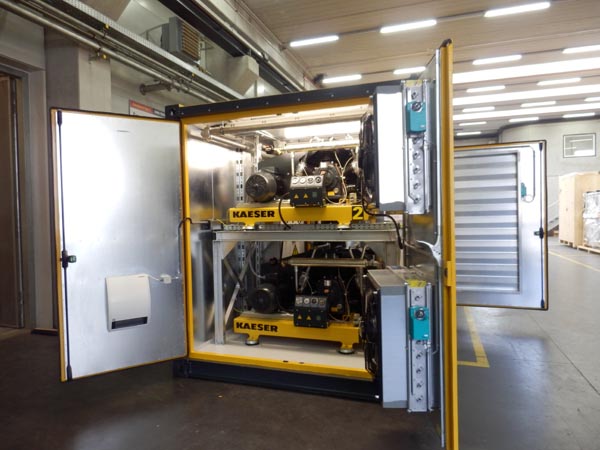
Pohled na boosterovou jednotku
(kompresory jsou umístěny nad sebou)
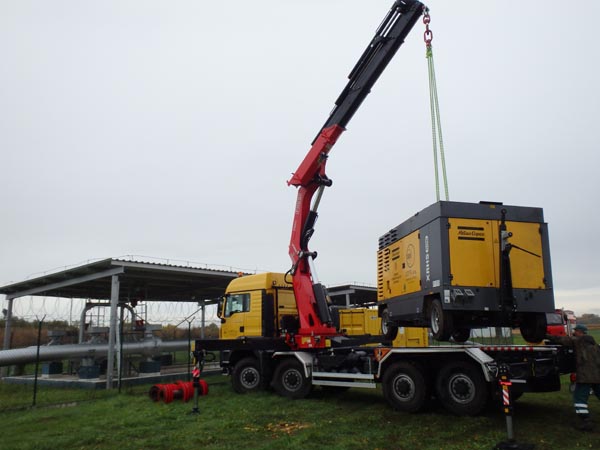
Kompresor procesního vzduchu
Meze výbušnosti hořlavých plynů a par
Významnou součástí projektu bylo i definování provozních režimů
zařízení. Podstatou inertizace potrubí je vytvoření takové
atmosféry v potrubí, kdy je koncentrace hořlavých plynů nebo
par mimo meze výbušnosti. Problémem však je, že s rostoucím
tlakem se meze výbušnosti rozevírají, především horní mez
výbušnosti poměrně značně roste. Zejména při vytlačování hořlavých
kapalin, kdy je vzhledem k hydrostatickému tlaku nutné
pracovat i s vysokými tlaky, je tedy třeba zvolit potřebnou
koncentraci dusíku v inertizační směsi v závislosti na
tom, jaký bude maximální tlak při vytlačování kapaliny. Navíc
záleží i na složení vytlačovaného média, jiné meze výbušnosti má
zemní plyn, jiné plynný LPG, jiné benzin a jiné nafta. Ještě
spletitější je případ ropy, která obsahuje jak lehké, tak těžké
složky, takže bezprostředně po vytlačení se do prostoru za ježkem
odpařují především lehčí uhlovodíky, zatímco po delší prodlevě se
odpařují uhlovodíky těžší.
Proto CEPS požádal pracovníky Ústavu plynárenství pražské VŠCHT,
aby se na projektu podíleli analýzou tohoto problému. Výsledkem
výzkumných prací byla definice různých pracovních režimů
v závislosti na složení vytlačovaného média a rozsahu
provozního tlaku.
Nasazení v praxi
Generátory inertizační směsi N-1100 byly poprvé provozně
nasazeny při pracích na části ropovodu DN 700, vedoucího od hranice
Lotyšsko/Bělorusko do přístavního Ventspils. Tento ropovod
v délce přes 250 km, jehož vlastníkem je společnost
LatRosTrans, byl dlouhodobě neprovozován a provozovatel se rozhodl
potrubí z ekologických i bezpečnostních důvodů vyprázdnit,
dokonale vyčistit od veškerých uhlovodíků a natlakovat inertizační
směsí o koncentraci dusíku 95 %.
Další rutinní nasazení při vytlačování hořlavých kapalin již běžně
probíhá na potrubích ropovodů českého MERO (viz obr. 5),
slovenského Transpetrolu i produktovodů ČEPRO.
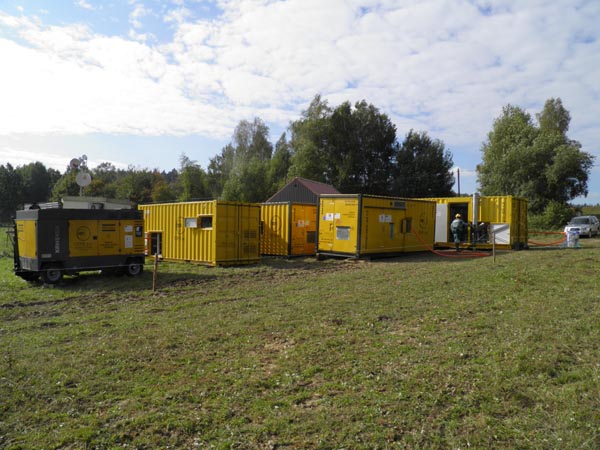
Provozní nasazení na ropovodu DN 700
MERO IKL
V Polsku bylo provedeno odplynění a inertizace dvou
vysokotlakých plynovodů (DN 500 a DN 200) před jejich
opravami, čímž se podařilo významně zkrátit čas, který by jinak
odplyňování a zajištění bezpečné atmosféry klasickou metodou
vyžadovalo. Zároveň zde proběhla inertizace i nově postavených
vysokotlakých plynovodů DN 700 a DN 800 před jejich
zprovozněním.
Začátkem léta tohoto roku proběhlo vyprázdnění 35 km potrubí
produktovodu DN 500 přepravujícího motorovou naftu na území
Běloruska pro společnost Transněftěprodukt.
V současné době CEPS disponuje třemi generátory dusíku a
dvěma boostery.
Závěr
Zavedení technologie vytlačování hořlavých plynů a kapalin
tlakovou inertizační směsí významným způsobem zvyšuje bezpečnost
těchto náročných prací. Navíc v případě odvzdušňování a
odplyňování plynovodů lze díky inertizační směsi bezpečně použít
oddělovací ježky, a tak podstatně urychlit jak odvzdušňování, tak
především odplyňování.
Autor: PR CEPS, Aleš Brynych, Petr Crha